LAST OF 4-PART SERIES
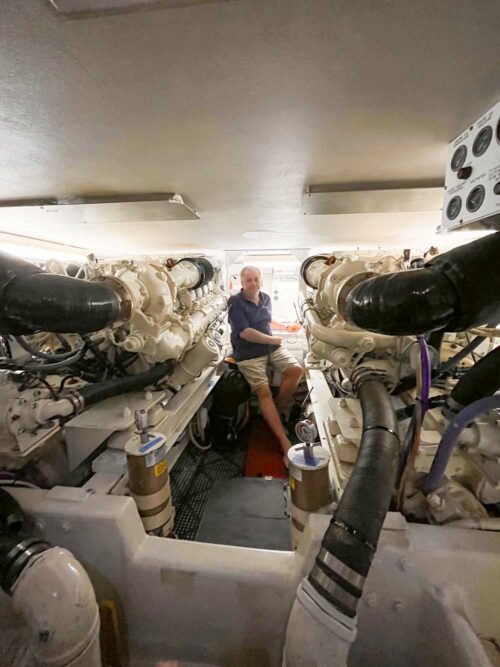
By Jeff & Colyn Fleming | 12V Marine
In recent weeks, many of you have seen articles about our experiences onboard ‘Icon of the Seas’ – the world’s largest (and newest) cruise ship. We are a father/son team, having worked on a multitude of different vessels: From an 8-foot dinghy to the 1,198-foot Icon.
Our understanding of electrical theory, troubleshooting, and installation has given us so many opportunities that we are beyond grateful for; however, to say that we don’t have our preferences in work would be a lie. Troubleshooting is our favorite, it requires a lot of thought and understanding of how systems (should) work. Don’t get me wrong, being paid to live on a cruise ship with an all-you-can-eat buffet and $2 drinks at the bar is great and all, but the work is redundant.
When you get on these ships that are ‘new builds,’ the problems they have are typically one mistake made 500 times. It’s like a very expensive game of relay, one guy is told how to do something, who then relays it to his team, some understand while others not so much. Next thing you know they set them free on a ship to go install the same thing in 1000 rooms, now 500 of those rooms have the same exact issue!
It’s our job to go fix that same issue over and over again and the only troubleshooting happens in the first case — the rest are rinse and repeat. Fortunately, we had a team on board to fix the redundant problems so we could move on.
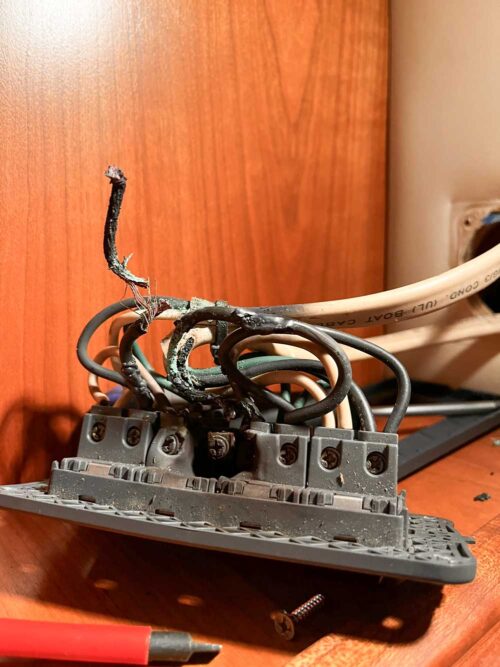
“Small” boats, however, are a different story. Installing upgraded new marine electronics is cool, but God only knows what is going on in the rat’s nest of wires behind the panels, causing issues that make absolutely zero sense, like cabin lights turning on chart plotters. This usually requires a great deal of thinking, testing, and head-scratching, especially in “new-to-me” boats without captains’ logs.
It is very scary how often we find burnt wires and melted fixtures while looking for other issues. And newer production yachts use glue to attach panels with no regard to access for future installations or troubleshooting amplifying the difficulty. However, to say we don’t learn a lot on these ships is far from the truth. Our ability to track down the damage from galvanic corrosion to a specific boat in a marina – derived from working on a cruise ship where chasing grounds leaks was our primary job (a similar process). These larger jobs help us figure out how to work and communicate (fancy word for ‘argue’) efficiently together. It also gives us opportunities to learn from others’ mistakes rather than our own, which gets old.
Our confidence, knowledge, and efficiency have given us opportunities to work on even bigger ships in the future. Many higher-ups from the shipyard that we worked with have specifically asked for our help with other cruise liners launching soon. And while we do prefer working on these smaller vessels, there’s something about the scale and daunting nature of these floating cities that lures us back.
Editor’s note: The Flemings are easy to work with. Call them at (252) 251-2900, or visit www.12vMarine.com